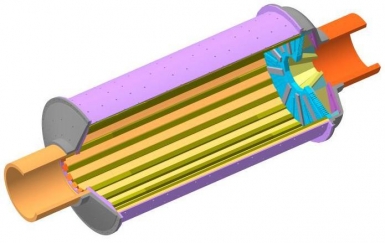
Complete set of rubber lining is used in the pebble grate mills at the grinding stages II - III (tumbling medium – ore pebble of 100 to 25mm in size) and includes head lining, discharge end lining (grate, elevator), shell lining and set of fixture elements.
Rubber lifter bars include directly vulcanized steel or aluminium armature.
Shell lifter bars are fastened with T-bolts М30, М36. End lifter bars are fastened with М36, М42 bolts.
Wear rate of elastic material grate is significantly lower as compared with metallic grate.
The elastic material grate process efficiency by the finished product grade yield is higher than that with the use of metallic grate.
Elastic material grate features self-cleaning capability.
Practical operation of rubber grates in the pebble grate mills at the Inguletskiy GOK has demonstrated that the “clear area” reduction by 30 - 40% had no effect on the mill process performance.
Elastic material grate service life is 1.5 - 2 times as that of metallic grate.
Elastic material elevator service life is 2.0 - 4.0 times as that of metallic elevator.
The mill tumbling medium is flint pebble in form of rounded pieces of 25 to 75mm in diameter.
Ground material is discharged through the slotted or round mesh screen installed upstream the discharge trunnion.
Between the screen and discharge end lid, elevator is installed with the radial fins dividing the plenum between screen and end lid into segment chambers open into the trunnion. During the shell rotation, fins elevate screened fine product to the discharge trunnion level. Such design provides maintaining the low pulp level in mill and reduces material residence time due to pulp volume reduction.
Important factor determining the ore-pebble mill performance is lining durability. Lining design and material determine mill turnaround time, its production output and specific power and tumbling medium consumption.
Ore-pebble mill operation experience has demonstrated low service life of wear-resistant steel linings. In addition, the screen mesh is plugged with pebble. Screen mounting bolts also fail prematurely due to abrasion with pulp.
All these disadvantages of ore-pebble mill operation became drivers for the new lining design and material development.
The use of rubber as material for making the ore-pebble mill lining has demonstrated as follows:
The rubber elevator used for ground product discharge from the mill offers following advantages: